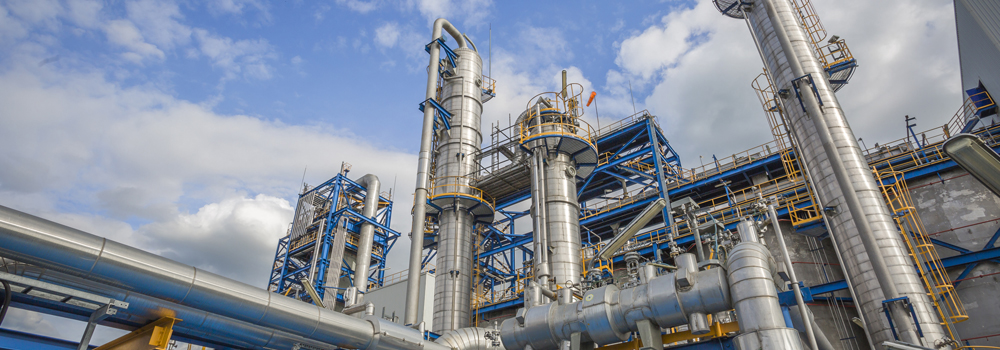
18 Mar Emergency Fluid Catalytic Cracking Unit Repair
Industry: Refining and Petrochemical
Description of Equipment: Fluid Catalytic Cracking Unit
Problem: Scheduled thermal imaging showed excessive hot spots in the FCC unit in various locations. Emergency refractory repairs were required to replace areas of damaged refractory.
Solution: Thermbrake 403-G lightweight insulating gun grade refractory was approved to repair the regenerator shell wall and Thermbond Formula 4-AG high density gun grade erosion resistant material was selected to repair the damaged refractory in the Spent Catalyst Inlet Line to the Regenerator. Thermbond’s unique binder system provided the desired chemical bond strength and quick dry-out to save time during this emergency repair. Thermbond Formula 12-L high erosion resistant rammable was also installed in the slide valve where extreme erosion resistance was required.
Product Being Replaced: Conventional light weight and high abrasion refractory materials.
Products Applied: Formula 4-AG, Formula 12-L, Thermbrake 403-G
Method of Installation: Gunning with Formula 4-AG and Thermbrake 403-G; Formula 12-L rammed
Equipment Used: Compressors, horizontal mixer, Stellar gunning box, Allentown gun, Hobart mixer
Scope of Work: Three areas needing repairs were discovered during unit inspection. Areas explored were those that showed hot spots from pre-shutdown Thermal Imaging. These areas were:
- Spent Catalyst Inlet to Regenerator – Thickness transitioned from 1″ to 5″ of Formula 4-AG
- Slide Valve Area – 3″ thickness of rammable Formula 12-L
- Regenerator Shell Wall – 5″ thickness of Thermbrake 403-G