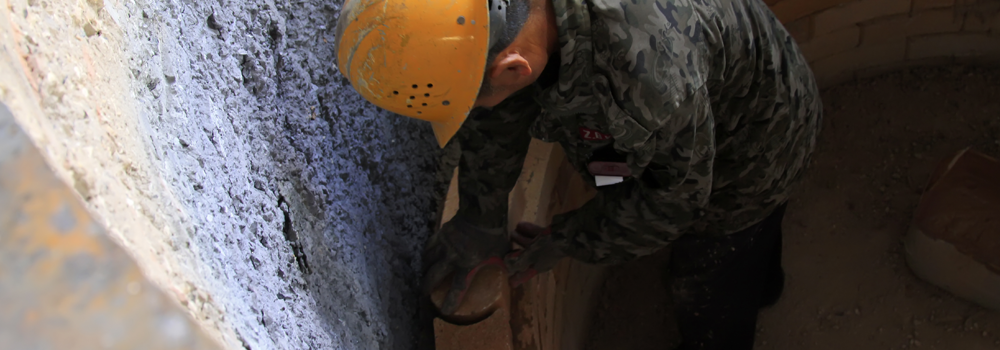
30 Jul Thermbond Provides Hot-to-Hot Full Furnace Reline
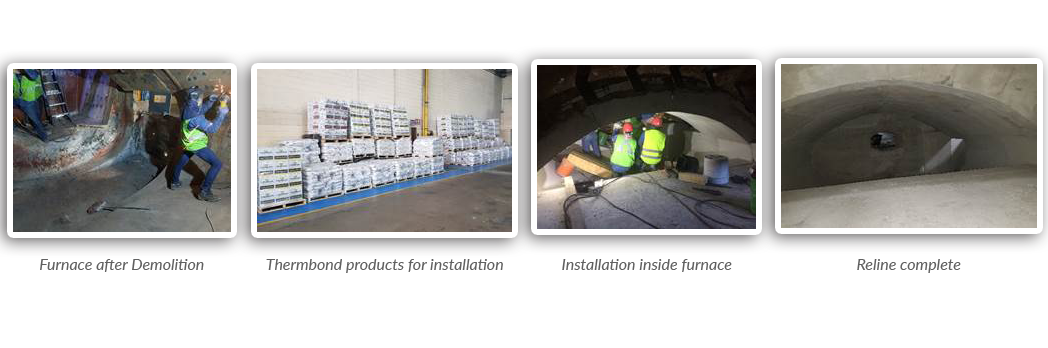
Industry: Aluminum
Description of Equipment: Tower Melter
Problem: Customer wanted improved furnace performance, less corundum build-up and increased life of the refractory lining.
Solution: Customer has utilized Thermbond technologies in other applications in their facility. Based on the exceptional service and successful performance of the products, Thermbond was asked to provide a HOT-to-HOT furnace reline. Thermbond Formula 3-E, 4-E, 5-E, 2104-L and Thermbrake 403-G were selected for this complete furnace reline. These products offered properties to extend the lifetime of the lining and reduce corundum build-up.
Product Being Replaced: Conventional refractory lining
Savings Using Thermbond: Thermbond’s properties decreased the installation time by 30%, getting the furnace back online much faster than conventional refractories would have.
Products Applied: 2000 units of Thermbond Formula 3-E, Formula 4-E, Formula 5-E, Formula 2104-L, Thermbrake 403-G
Method of Installation: Cast, Vibrated
Equipment Used: Mixer, vibration equipment
Scope of Work: The customer turned the furnace over to Thermbond for relining once aluminum was completely removed from the furnace. The furnace was cooled down, the old refractory lining was then torn out, shell repairs were made, and the furnace was completely relined with Thermbond products. When forms were removed and burners reconnected, Thermbond monitored the dry-out of the furnace. Once the lining was completely dried out, the furnace was given back to the customer at operating temperature. Thermbond provided a turnkey service from Hot to Hot. Thermbond installation support was on site to provide dry-out supervision.
Installation Date: October 2018
Follow Up: Furnace continues to perform well. Success of this installation has resulted in additional opportunities for Thermbond products at this facility.